In industrial piping systems, ball valves are essential for controlling the flow of liquids and gases.
Among the various configurations, long-pattern and short-pattern ball valves stand out for their distinct designs and applications.
These terms refer to the length of the valve’s body as specified by standards like ASME B16.10, which governs face-to-face and end-to-end dimensions for valves.
Whether you’re optimizing space in a tight installation or prioritizing durability and flow efficiency, understanding the differences between long pattern vs short pattern ball valves can help you make informed decisions.
What is a Long Pattern Ball Valve?
A long-pattern ball valve features an elongated body design, offering greater face-to-face dimensions than its short-pattern counterpart. This type of valve is built to handle heavy-duty industrial applications.
Design Characteristics
- Extended Length: The valve body is longer, providing a more robust structure.
- Flow Efficiency: Due to the increased length, the internal passage typically ensures smoother and more consistent flow with minimal turbulence.
- Standards Compliance: Long pattern ball valves are often manufactured to comply with ASME B16.10, ensuring uniformity in dimensions across industries.
Applications
- High-Pressure Systems: The durable design makes these valves ideal for high-pressure pipelines.
- Refineries and Petrochemicals: Long pattern valves are widely used in oil refineries due to their robust construction.
- Corrosive Environments: With proper materials, these valves can withstand harsh chemicals.
What is a Short Pattern Ball Valve?
A short pattern ball valve has a compact body design, making it lighter and easier to install in tight spaces. This design is often used where space constraints are a primary concern.
Design Characteristics
- Compact Size: The shorter face-to-face length minimizes the valve’s footprint.
- Cost Efficiency: Short pattern valves generally require less material, making them more economical.
- Quick Installation: Their smaller size simplifies installation and maintenance, especially in confined areas.
Applications
- Tight Spaces: Ideal for systems where space is limited, such as shipyards or small processing units.
- Moderate Flow Systems: Suitable for pipelines with moderate pressure and flow requirements.
- Temporary Installations: These are commonly used in applications where frequent replacements or relocations are needed.
Long Pattern vs Short Pattern Ball Valve: Key Differences
Feature | Long Pattern Ball Valve | Short Pattern Ball Valve |
Size and Length | Longer face-to-face dimensions | Compact and lightweight |
Flow Characteristics | Superior flow efficiency with minimal loss | Moderate flow efficiency |
Cost and Space | Higher cost, occupies more space | Cost-effective, space-saving design |
Pressure and Temperature Handling | Suitable for high-pressure, high-temperature systems | Best for moderate pressure and temperature conditions |
Size and Length
Long pattern valves have an extended body, which increases their weight and the space they occupy. Short-pattern valves are more compact, making them ideal for confined installations.
Flow Characteristics
The longer internal passage in long pattern valves allows for smoother and more consistent flow. Short pattern valves may cause slightly more turbulence but are sufficient for standard flow conditions.
Cost and Space
Long pattern valves are costlier due to their larger size and more extensive material use. Short pattern valves, being lighter and smaller, are more budget-friendly.
Pressure and Temperature Handling
Long-pattern valves excel in high-pressure and high-temperature environments, while short-pattern valves are designed for moderate operating conditions.
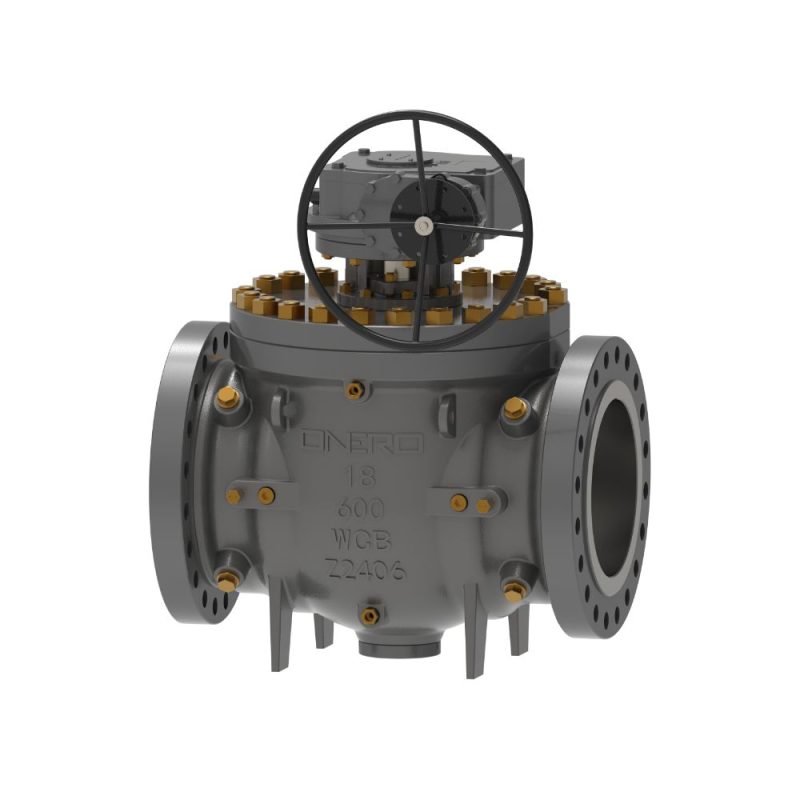
Top-entry, corrosion-resistant design. Easy maintenance. 1/2″–48″ size, 2500LB.
View Product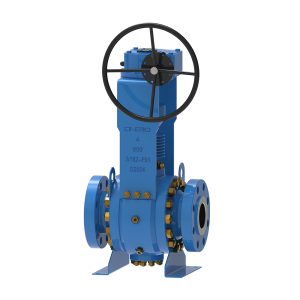
Withstands up to 500°C. Ideal for oil, gas, acid systems. Manual or electric drive.
View Product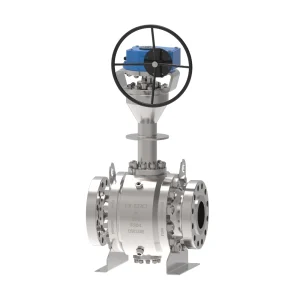
Works at -196°C. For LNG, cryogenic gas, chemical processes. 1/2″–48″ range.
View ProductASME B16.10 and Its Role in Valve Design
ASME B16.10 establishes the dimensions for face-to-face and end-to-end measurements in valves, which ensures compatibility across systems.
Both long and short-pattern ball valves adhere to these standards, enabling engineers to design systems with consistent and predictable specifications.
This standardization simplifies the replacement process and ensures that valves meet the necessary pressure and temperature ratings for their intended use.
When to Use Long Pattern vs Short Pattern Ball Valves
When to Use Long Pattern Ball Valves
- High-Duty Operations: Opt for long pattern valves in systems requiring high durability and reliability, such as oil and gas pipelines.
- Corrosive Media: Their robust design and material options make them suitable for chemical and corrosive environments.
- High Pressure: Choose these valves for pipelines operating under high pressure to ensure long-term performance.
When to Use Short Pattern Ball Valves
- Space-Constrained Installations: Ideal for compact setups where space is limited, such as machinery and shipyards.
- Cost-Sensitive Projects: These valves are cost-effective, making them suitable for projects with tight budgets.
- Frequent Maintenance: Their smaller size makes them easier to replace or service in systems requiring regular maintenance.
Long Pattern vs Short Pattern Ball Valve: Conclusion
Understanding the differences between long-pattern and short-pattern ball valves is crucial for selecting the right valve for your system and industries, in general.
Long-pattern valves excel in durability and flow efficiency, making them ideal for high-pressure industrial applications.
Short pattern valves, on the other hand, are compact, economical, and suited for installations with limited space.
By evaluating factors such as pressure, temperature, and space constraints, you can make an informed choice to optimize your piping system’s performance.